Driver’s view: Claas Trion 750 rated after two seasons’ work
The launch of the Trion combines two years ago represented one of the biggest-ever shake-ups of the Claas range.
Slotting between the high-output Lexions and late-of-this-parish Tucanos, they promised something for everyone.
As such, they come in 14 different flavours, or 20 if you include Terra Trac models – starting with the small, five-walker 520 and topping out at the twin-rotor 750.
This runs the same APS primary threshing system as the 740, 750 and 760 Lexions, paired with two 4.2m-long rotors housed inside a narrow body, offering many of the perks of its big stablemate in a slightly more affordable package.
One of the first Trion 750s to land in the UK wound up at Sentry Cambridgeshire, which has roughly 600ha of combinable crops to cut annually.
Farm manager Peter Keates gives us the lowdown on its performance after two seasons’ work.
See also: Driver’s view: Steve Bushell rates his New Holland CH7.70 combine
Sentry Cambridgeshire’s Claas Trion 750 Terra Trac
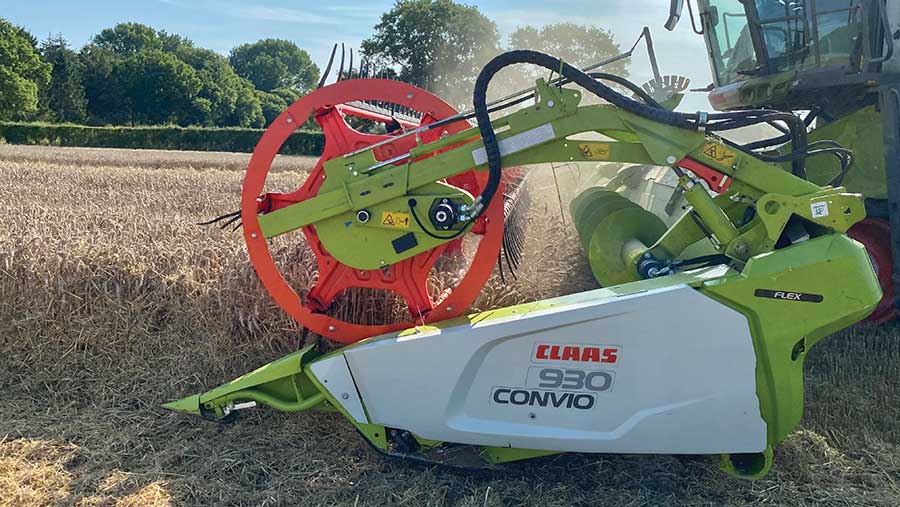
© MAG/Oliver Mark
- Year 2021
- Engine 8.9-litre Cummins L9
- Max power 435hp
- Threshing system APS primary thresher and twin rotors
- Rotor length/diameter 4.2m/445mm
- Header 9.3m Convio Flex 930
- Grain tank capacity 12,000-litre
- Approximate on-farm price (for 2024) £350,000 (including header)
What made you choose a Claas Trion 750?
The decision was made before I joined the business just over a year ago.
Its predecessor, a 2014 Claas Lexion 750, was due for replacement and Sentry was offered the chance to lease a pre-production Trion 750 Terra Trac, which arrived midway through the 2021 harvest.
It seems a good fit, as we’re cutting about 600ha a year and, for that sort of area, it offers a decent balance of output and cost.
The fact that the Trion effectively has the same APS threshing unit, twin rotors and hosepower as the old Lexion means we can cover a big area without having to cut when it’s wet.
However, it’s still a lot to ask of a single machine once you’ve factored in the commutes between the three farms I manage, at Chatteris and Conington Fen (Cambridgeshire), and just north of Downham Market (Norfolk).
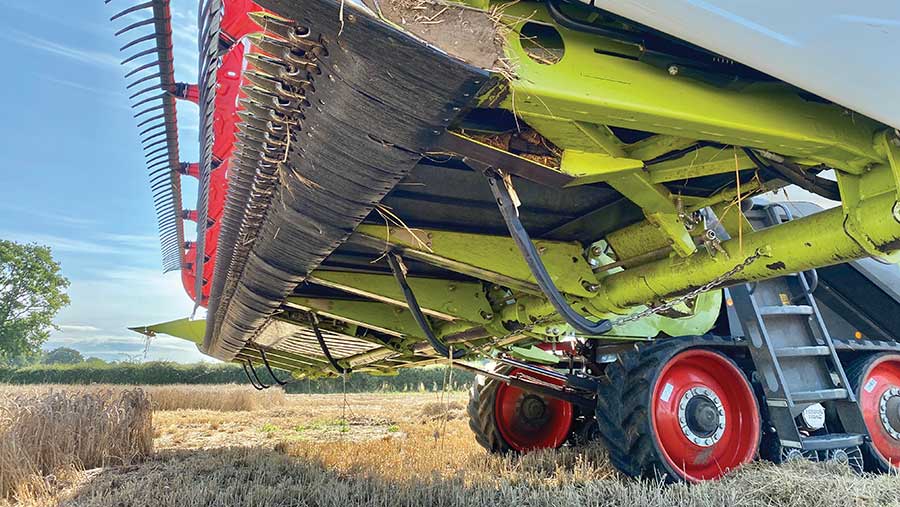
© MAG/Oliver Mark
What header does it have?
The draper-style, 9.3m-wide 930 Convio Flex header is as much a selling point as the Trion’s internals.
The belt-fed system is unbelievably good at picking up flat crops without taking a load of soil with it, and it often gets me out of trouble. I certainly wouldn’t want to go back to a regular auger header.
For the most part, I run it in Auto Contour mode. This keeps the table rigid, with the sensing arms underneath maintaining a consistent cutting height.
One improvement over previous Claas machines I’ve operated is that these arms are now plastic and have far more give in them.
I have bent the old metal ones in the past, usually when I reverse in a hurry without the chance to lift the table clear of the ground.
I only use the header in “flex” mode to pick up particularly flat or low crops, of which there has been very little this year – aside from a bit of winter barley.
It does a phenomenal job and saves fitting crop lifters, though the little plastic skids behind the knife section do wear. I replaced a dozen last year.
The main lateral belts feed the crop head-first, and smoothly, into the feeder house via a central intake belt.
Handily, this has a simple stone trap, which gives me a bit of time to spot something – usually bog oak on the peaty soils of the fens – before it goes up the elevator.
I have had occasional problems with material getting dragged underneath the central belt and jamming between it and the belly plate below, but it doesn’t take long to loosen the 13mm bolts and clear the blockage.
Another improvement is that the retractable auger fingers now clip into place, which saves fiddling around with a 10mm spanner should one break.
What is it like to operate?
This machine has Cemos Automatic, which provides settings for different crop types. I tend to use these to get going, then play around with them to clean up the sample, reduce losses or increase throughput.
It also has the Cruise Pilot speed control system, but I use this less frequently. It certainly gets the combine zipping along, but I’m a bit old-fashioned and I prefer to drive at a speed I feel suits the conditions.
The one thing it’s particularly good for is unloading, as it will maintain a set forward speed once the auger is out to make life easier for the corn cart driver.
I’ve also got a camera on the end of the pivoting spout and another at the back to help reverse, so visibility-wise I’m pretty well catered for.
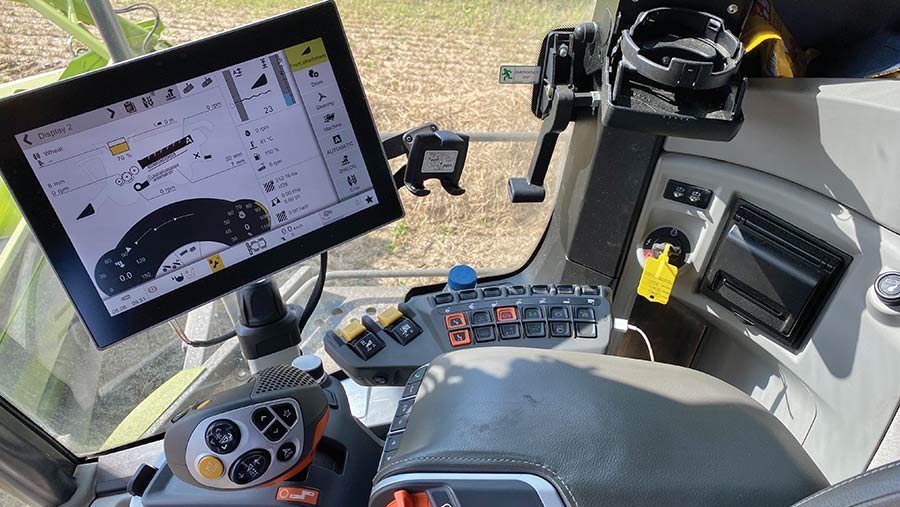
© MAG/Oliver Mark
How is the cab?
There’s little to fault it – it’s big and bright, the lights are great, and the seating position gives a good view of the whole header.
I certainly appreciated the comfort last year, as I was getting up at 3.30am to cut the oilseed rape during the hot weather, moving the machine during the day and then cutting wheat through the night.
Running on the satellite-based GPS Pilot system helps keep fatigue to a minimum, too.
How much can you cut in a day?
I’ve done a few 40ha days with it in wheat and, in a decent 9t/ha crop, I can get through 35-40t/hour.
It’s pretty good on fuel too – unless I’m running the chopper. In less favourable conditions, chopping straw can almost double the load on the engine.
This year it was particularly noticeable with the wetter-than-normal oilseed rape. It won’t be a problem for the wheat though, as an AD plant is willing to pay good money for baled straw.
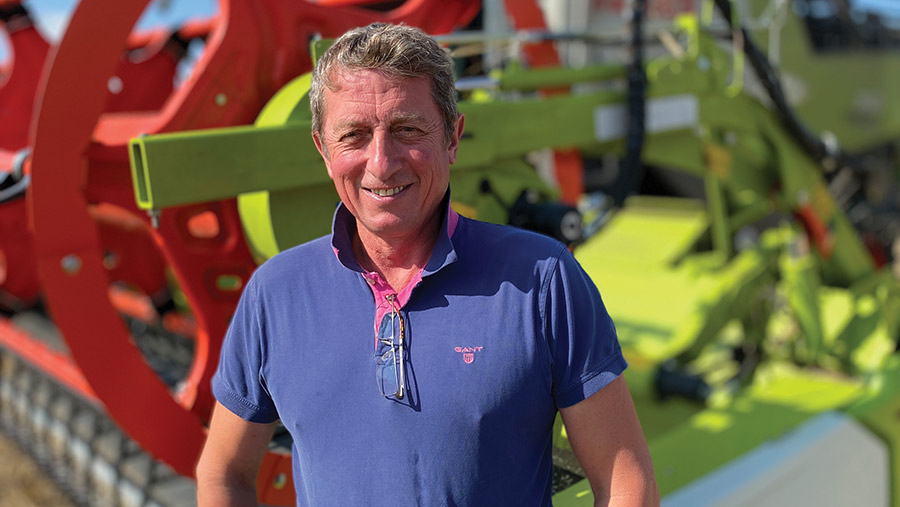
Peter Keates © MAG/Oliver Mark
Has it been reliable?
As it was a pre-production machine, Claas spent the winter of 2021/2022 fitting a load of modifications.
Some of them were necessary, such as tweaks to the grain pans to eliminate wastage and a new header tank on the radiator.
But they also replaced the seat and changed the air-conditioning, both of which seemed fine as they were.
We’ve had a few other niggles, most of which have been sorted overnight by Manns, our local dealer.
They include a main drive pulley shearing off, a problem with the alternator, and an issue with the unloading auger.
The latter wouldn’t locate into the crescent-shaped receiver in its closed position, so Claas changed some of the bracketry below to ensure it all lined up.
What could be improved?
I wish it was 40kph. It’s so slow on the road and it can take me two-and-a-quarter hours to complete the 40-mile run from the farm at Downham Market to Conington Fen.
As it takes so long, I’m moving towards block cropping the different farms so that we can systematically work from site to site rather than darting back and forth during harvest.
Would you have another?
Sentry almost exclusively runs Claas combines, so it’s likely that we’ll have the same again.
Size-wise it’s about perfect for our acreage. The threshing system and, in particular, the sieves wouldn’t take a bigger header and we don’t need one, as it would become too impractical for the fields we work.
But the decision won’t be made for a few years yet. The typical replacement policy is five years – but that has been pushed to seven to manage rising machinery costs.