Herts contractor builds novel self-propelled bale chaser
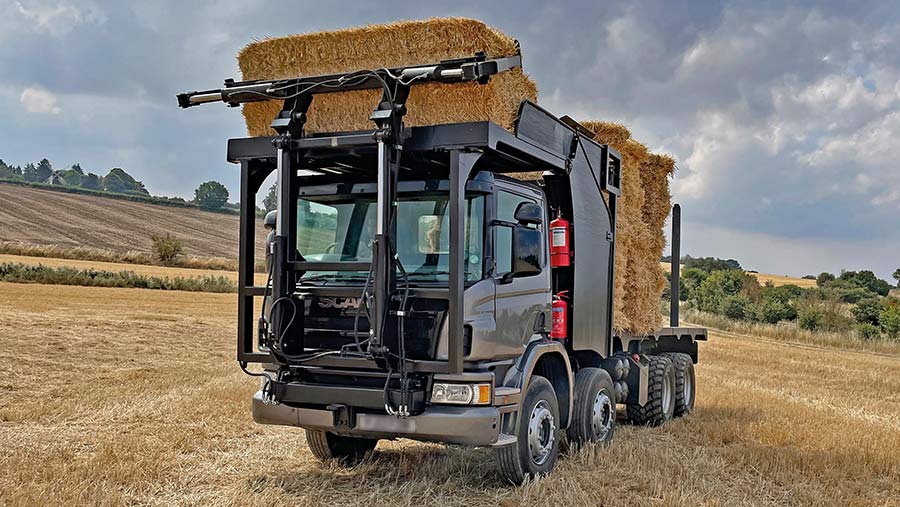
For years, farmers, contractors and machinery manufacturers have been dreaming up novel ways to make the job of hauling bulky straw bales more efficient.
Their endeavours have spawned high-capacity grabs, trailers with hydraulic sides for securing loads and umpteen elaborate chasers for collecting and stacking without the need for a loader.
But despite all this innovation, Joe Williams of Eastern Counties Straw could see room for improvement.
See also: Wiltshire contractor builds one-of-a-kind bale chaser
Having run 16-bale Heath Super Chasers for several years, he wanted a faster and more reliable way of corralling the 120x90cm bales produced by his eight-string Krone balers.
His first attempt was to double capacity, building a behemoth trailed chaser with a tri-axle chassis that could accommodate 32 bales in a single load.
It worked well enough, but it was too heavy to pull in anything but bone-dry conditions, even with a 300hp Fendt on the front.
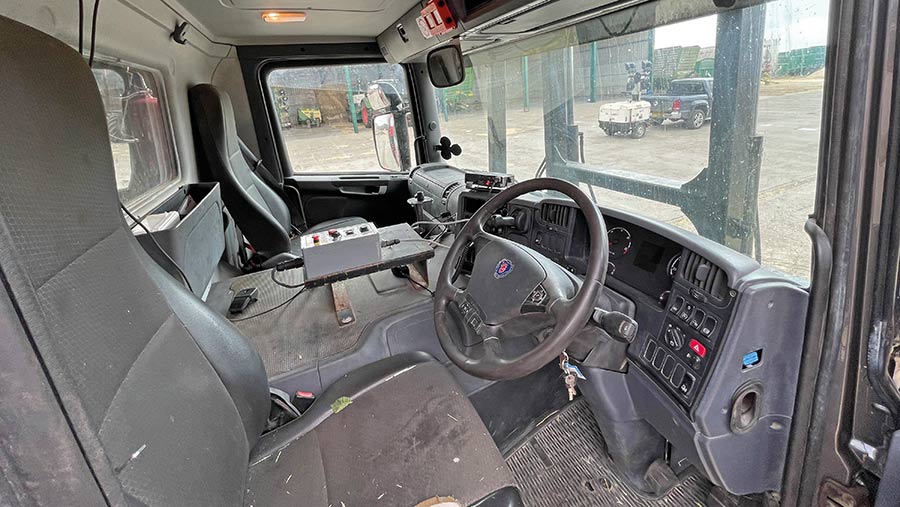
Cab interior © James Andrews
Instead, he turned his focus to making the job of collecting 16 bales quicker and more reliable.
To do this he decided to develop a self-propelled bale collector based on an eight-wheel lorry, rather than making an implement to pull behind a tractor.
He had seen examples built in the US and Australia that produced a single-row stack, but he reckoned he could go one better and fit a double row on the rear deck.
After a few sketches and a couple of miniature mock-ups, Mr Williams put the build in the hands of engineering whizz Tim Ansell, who runs Eastern Counties Straw’s sister business, JW Fabrications.
Mr Ansell cut his teeth building and maintaining gold mining equipment but has been working for the firm making and fixing agricultural machinery for the past 15 years (see “JW Fabrications” below).
The project was ready for testing in the 2021 season, but it has been properly working this year, shifting more than 4,000 bales.
JW Fabrications
JW Fabrications is the engineering arm of Eastern Countries Straw, specialising in building, modifying and fixing agricultural machinery.
Much of its work is for the straw business, but it carries out some jobs for other contractors and farmers.
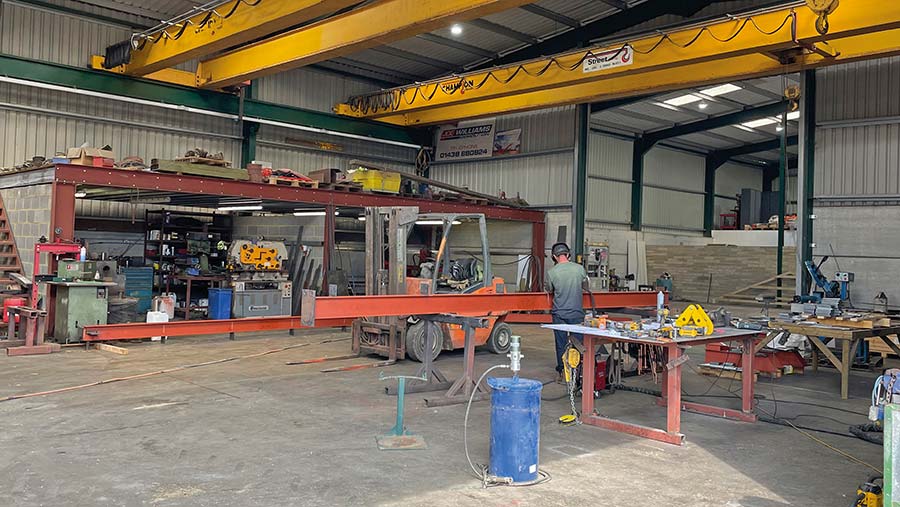
JW Fabrications’ workshop © James Andrews
Past projects include a silage elevator that allows maize to be loaded into trailers waiting on the roadside to avoid getting mud on the road.
The first was built for the firm’s own use, but its success sparked sufficient interest for them to build a couple more.
Since then, it has fashioned another iteration based on a large snow blower.
The attraction of this is that it has an adjustable spout so that trailers can be loaded evenly without having to shunt them back and forth.
Engineer Tim Ansell and his team have also come up with a custom service trailer for the business that travels with them during the maize campaign.
It’s based on a tri-axle chassis and accommodates a 10,000-litre diesel tank, AdBlue storage, generator, telescopic floodlight, and a couple of pressure washers, as well as a comprehensive set of tools and… a gas barbecue, of course.
How it works
At the front of the lorry there’s a hydraulic arm that grabs bales and drops them onto a hinged platform on the cab roof.
This then lifts at the front, forming a ramp that the bales slide down before landing on their side on the rear deck.
Another bale is dropped onto the first, forming a double layer, before a hydraulic headboard shunts them down the bed, making room for the next pair.
To prevent the first row of bales toppling over, hydraulic fingers lift out of the bed to secure them as they fall into place.
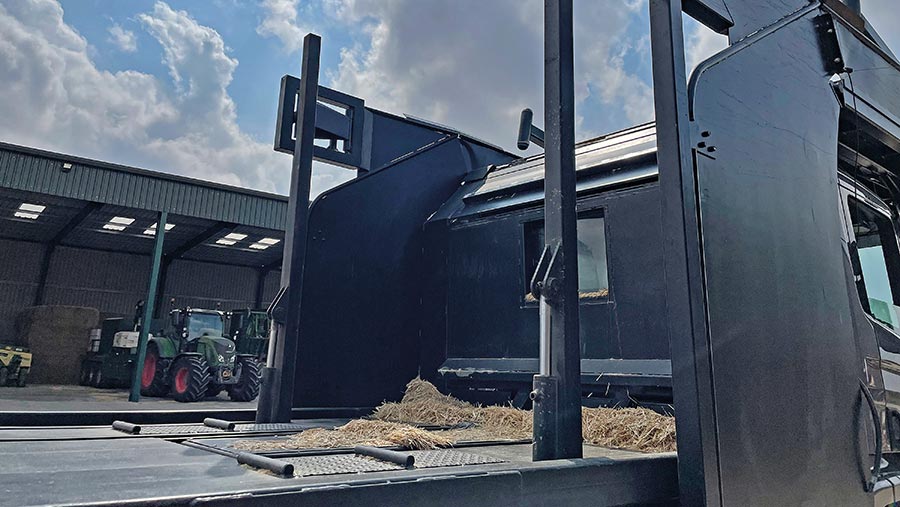
Loading mechanism © James Andrews
These then drop back down, allowing the bales to be pushed back. Eight rows are accommodated in this way, giving a total capacity of 16 bales.
When it comes to unloading, the whole bed tips up so that the bales can be deposited vertically.
At the same time, a couple of flaps pop out the floor to step the top half of the load, making for a more stable stack.
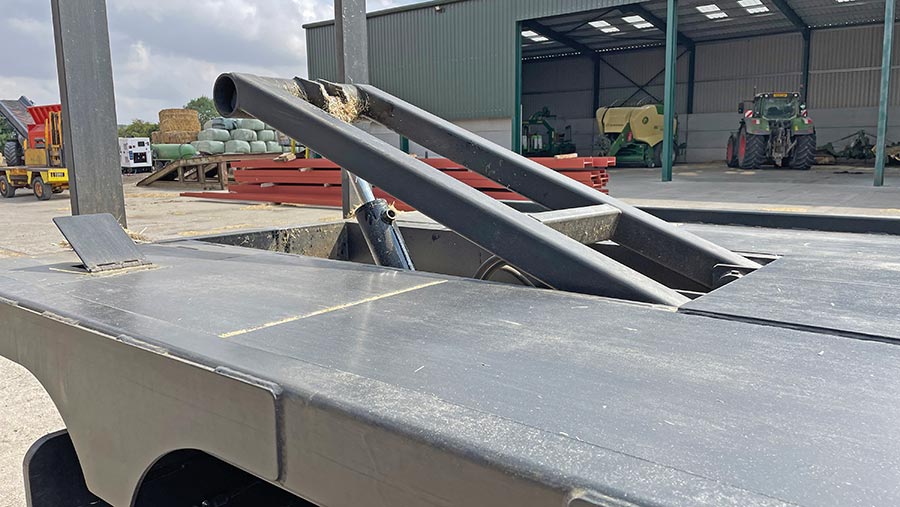
Bale pusher © James Andrews
There is also a hydraulic arm at the bottom of the bed to help push the load into the stack as the driver pulls away.
All functions are controlled by a single electronic joystick mounted on the driver’s door, so it’s simple to operate.
Faster loading
The capacity of the lorry might be the same as the firm’s trailed chasers, but it can collect considerably more bales in a day.
There are a couple of reasons for this. First, the lorry is compact and has good suspension, meaning it can nip through tight entrances easily and cruise along rough ground at speed without running the risk of knocking bales over, or rattling the operator’s teeth out.
“You can hammer down the field at 50mph if you want,” says Mr Williams.
But the biggest bonus is the fact that it makes consistent stacks that are stable and rarely fall over. The secret to this is the front loading arm, which centralises each bale as it is picked up.
This means there’s no margin for error, unlike many other chasers, which require some operator skill to jab the loading spike into the bale at the correct point.
Fuel use is also considerably lower than a tractor and trailed chaser, using about 200/litres for a full day’s shift.
Building it
The lorry chaser is based on a 2013 Scania eight-wheeler that had been used as a dust cart with an up-and-over loader on the front.
None of the original mechanism was used for the bale chaser project, but this model was attractive as it had a large spool block with air solenoids that could be used to run the complex hydraulic services.
With the lorry stripped back to its chassis, Mr Ansell and his team set about fabricating the chaser.
This started with the loading arm, which, thanks to its complex geometry, was built up as a scale model before proper fabrication began.
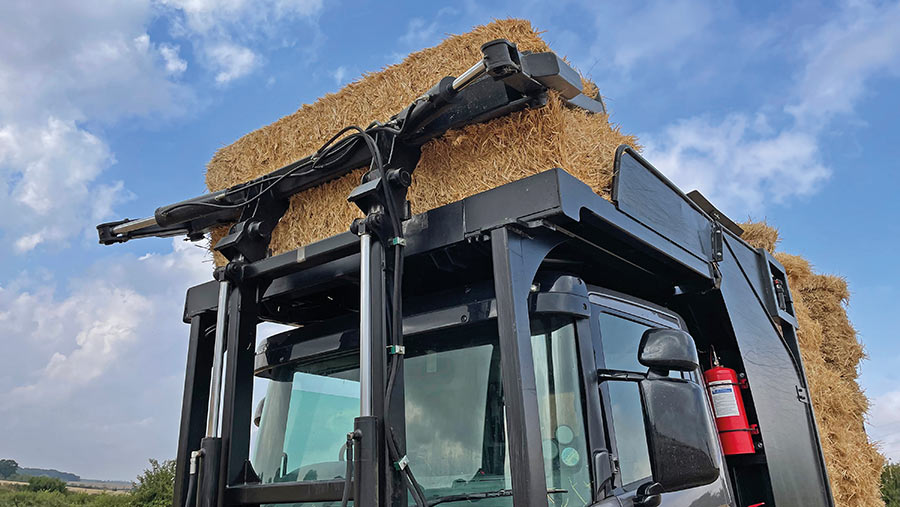
Bale loading arm © James Andrews
Cleverly, the arm can move in a wide arc, allowing it to drop down to the ground to pick up a bale and then lift vertically so that the load is at roof height.
The hydraulic gripper arm is a neat design too, with a pair of linked hydraulic rams that mean the bale is always secured in the centre.
Also, when the arm is raised to full height, the grab is weighted so that the bale flops back onto the roof platform.
Getting the roof platform to lift high enough for the bale to slide off and onto the rear bed was one of the biggest headaches, largely because there’s such a small space to squeeze the rams between it and the cab roof.
Eventually they managed to get the angles right, so that the platform fires up rapidly to dislodge the bale from its perch.
Compared with the front end, the rear load area was a more straightforward fabrication job. However, a good deal of thought went into some of the finer details.
These include the securing fingers that stop the first row of bales falling over backwards, some sprung lugs on the side of the frame to stop them tipping forwards, and the stack stepping plates in the base.
All new steel was used in the build and many of the sections were cut on an Esprit Automation profile cutter.
Mr Ansell produces the CAD drawings for this himself, so the project was put together without outsourcing much of the work.
However, with a dozen or so hydraulic rams on board, the team drafted in some help to get the system plumbed in efficiently.
This job went to retired electronics engineer and hydraulics specialist Phil Nelson, who was able to get a small, computer-style joystick to talk to the lorry’s air solenoid spool block.
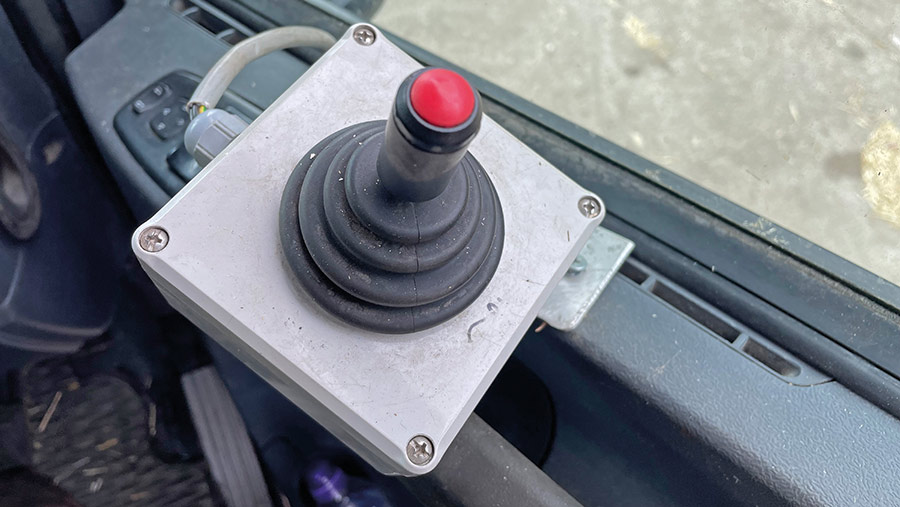
Joystick controller © James Andrews
The finishing touch was to fit an automatic fire suppression system with tubes that rupture in the event of a fire and spray suppressant around the machine.
They also had a custom tarpaulin made that sits at the back of the cab to prevent flammable debris collecting.
Modifications
At present, the hydraulic system is semi-automated, with a series of flow restrictors to make certain rams move before others.
However, the next step is for Mr Nelson to fully automate it, so that no operator input is required once the bale has been picked up.
Plans are also in place to fit the lorry with a reversing fan to help keep it cool in dusty conditions.
The chaser has been built as a demount unit, so it can easily be unbolted and removed.
To make better use of the lorry, Mr Williams is hoping to fit it with a Bergmann muckspreader and possibly a silage body so that it can haul grass.
Agricultural use
Registering the truck as an agricultural vehicle means it can be run on red diesel and driven by any operator.
The rear wheels have also been replaced with chunky rims shod with BKT 560/45 R22.5 tyres to help spread the weight and make it travel better on rough ground.
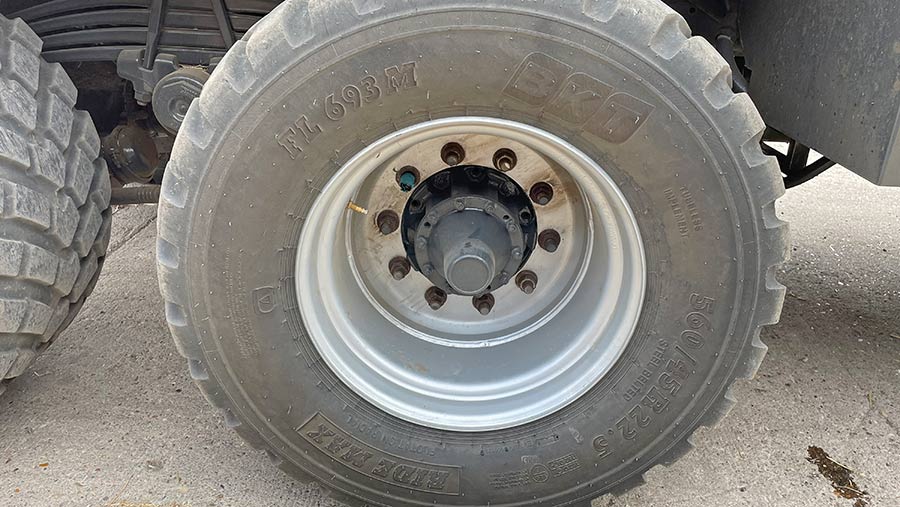
© James Andrews
At the front, both axles are running the original 295/80 R22.5s, but the plan is to upgrade these to 500mm tyres – the largest that will fit without running the risk of rubbing when turning.
The truck isn’t all-wheel drive, but both rear axles are driven and there is a diff-lock if it’s required.
Traction hasn’t been a problem for the past two years and Mr Williams reckons it’s competent enough to cope with ground conditions at harvest, even in years when the going is soft.
Building to order
Now that the design has been perfected, JW Fabrications is open to building similar examples for other contractors or hiring them out.
Prices are likely to be around the £120,000 mark, plus the price of a donor lorry. As a guide, the 2013 Scania used on this first machine cost about £20,000 with 100,000 miles on the clock.
The chaser is designed for 120x90cm bales, but it can be adapted to work with most sizes.